BETA SUCCESS STORY
30% REDUCTION
IN PREPARATION TIME FOR AUDITS
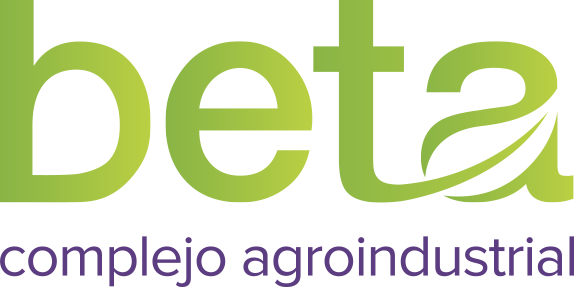
30% reduction in information collection and presentation times
Agroindustrial Beta reduced the time for collecting and presenting information for internal audits by 30%.
Time for collecting and preparing information for internal audits was reduced in 30%.
Quality inspections were digitized, generating efficiencies and traceability throughout the entire process.
It became easier for supervisors to collect and share information regarding quality inspections in the packing operation.
Introduction
Agroindustrial Beta (https://beta.com.pe/) is a Peruvian company dedicated to the cultivation, packing and export of asparagus, tangerines, blueberries, grapes, avocados and pomegranates. They have 43 farms and 9 packing plants distributed in agricultural areas throughout the country and send their products to 40 export markets.
The objective of this case study is to demonstrate how the use case: "Quality Inspections", within the Packing Module, generates a real and tangible benefit for agricultural producers.
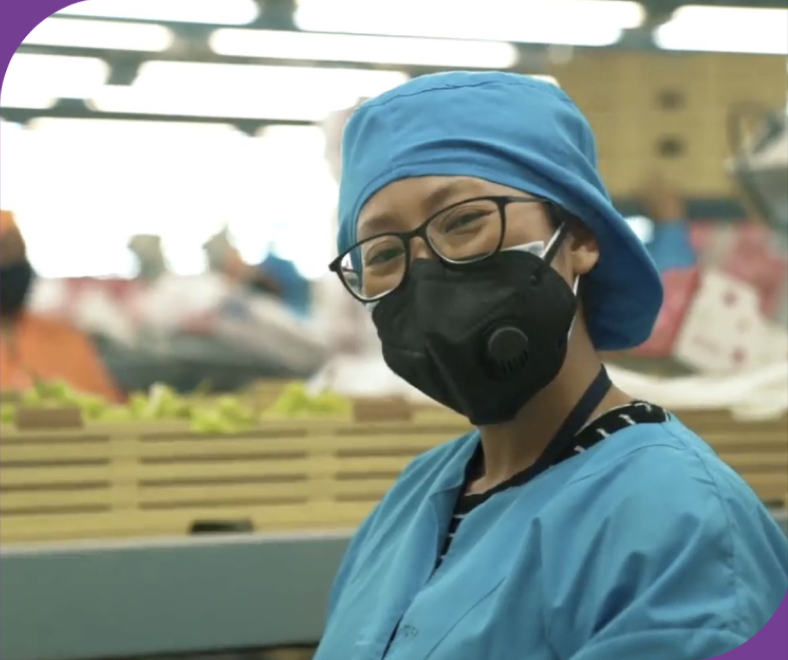
Problem statement
Manual information collection methods make traceability and the ease of quickly sharing information complicated. This can generate wastes such as delays in collecting traceability information.
The primary inspection record forms were filled out manually; this information had to be transcribed into Excel to generate reports that made it difficult to quickly share information to make effective and timely decisions.
Filling out forms manually generated disadvantages such as the following:
- Difficulty sharing information quickly or immediately
- Risk of errors: When recording information manually and then transcribing it and transferring it to an Excel report, the possibility of error increases.
- Limited traceability: Not having the information digitized can limit the traceability in time or availability of the information.
Solution
The implementation of the use case: "Quality Inspections", of SpaceAG's Packing Module, allowed the client to digitize the quality evaluations in the blueberry packing process. SpaceAG's mobile app replaced pencil and paper, allowing data collection using cell phones or tablets. With this information, we implement digitalized formats and reports that allowed the data to be viewed in real time and quickly shared with other areas or interested stakeholders. In this way, the client's work was made easier, they obtain information faster and are able to share it easily, they can also act in a more timely manner and make decisions based on data.
Use case: Quality Inspections in Packing:
Speeds up the process of capturing and processing information in packing through digital forms, formats and reports accessible through the digital platform and stored in the cloud.
Implementation
The implementation included the following activities:
- Creation of supervisor and evaluator users with different permission levels (administrator, editor, viewer).
- Creation of quality evaluation forms.
- Creation of evaluators or monitors with access codes to the SpaceAG application.
- Assignment of evaluators to created forms.
- Training evaluators to understand the data capture process and upload information to the software.
- Generation of digitized formats under the client standard that allow information captured in the packing operations to be displayed in real time.
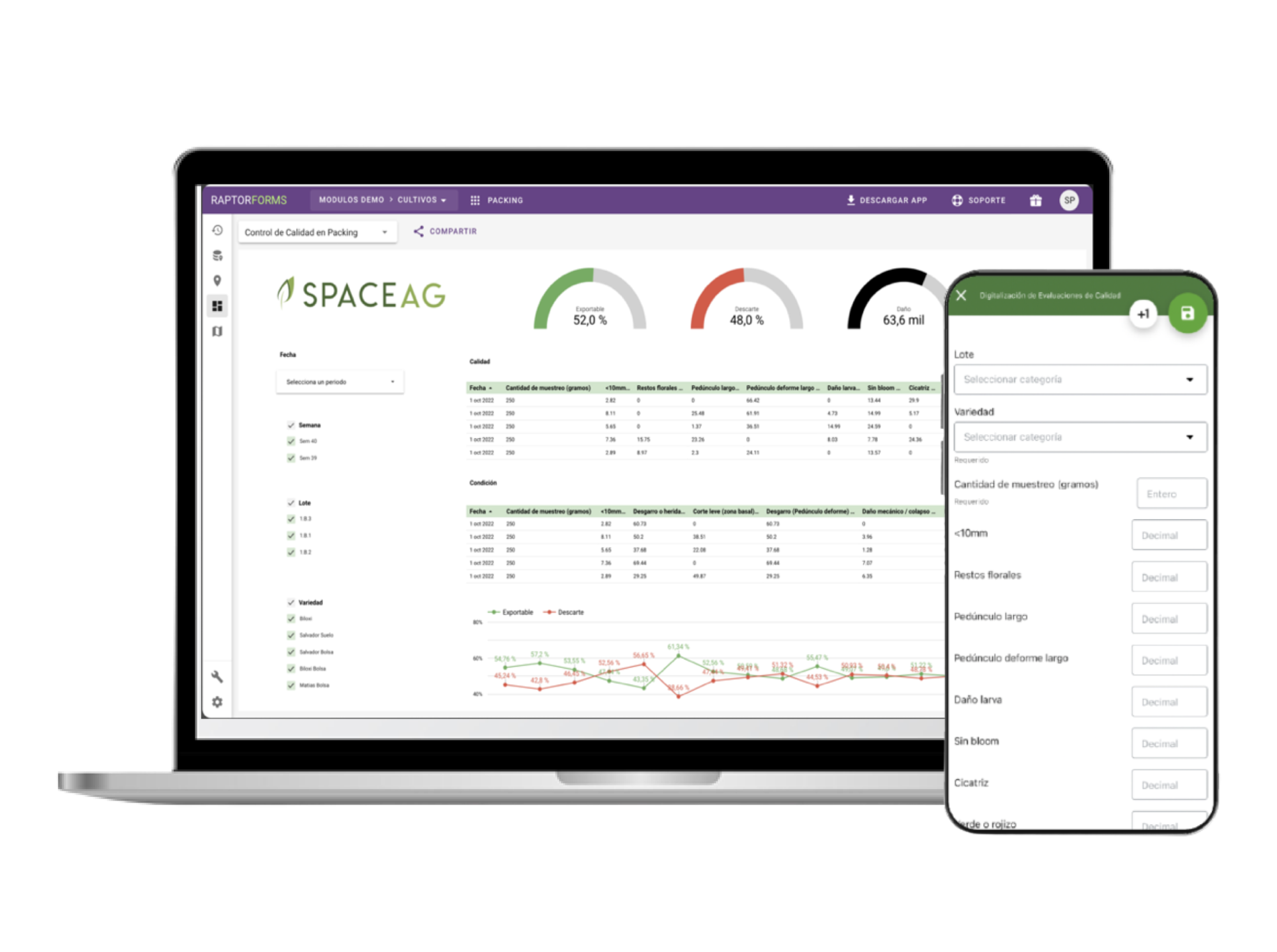
Results
Digitizing quality assessments helped the client:
- Generate efficiencies and traceability throughout the entire process.
- Facilitate the work of supervisors to collect and share information on quality evaluations in packing.
- Reduce by 30% the time of collecting and preparing information for internal and external audits.
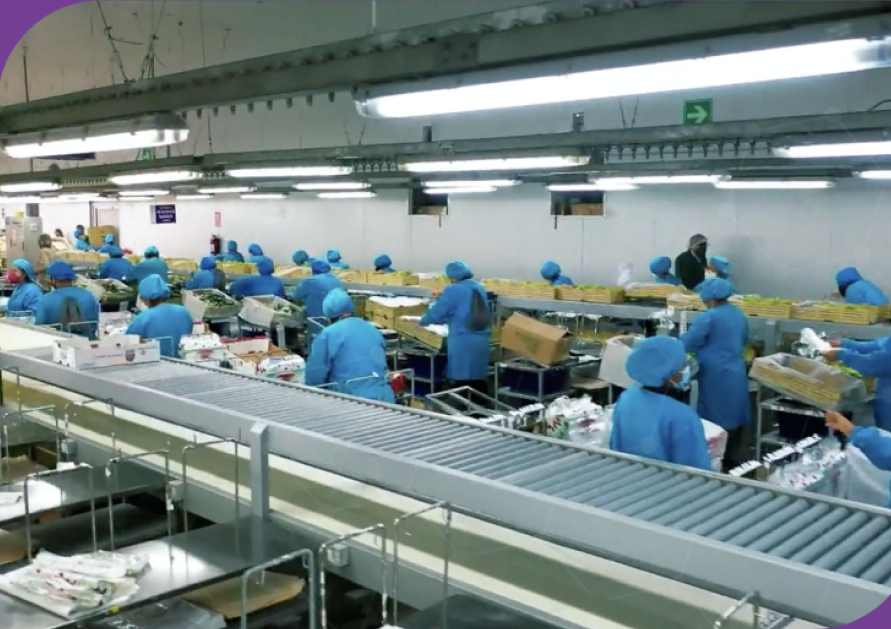
ROI Analysis
Costs associated with the implementation of the Packing Module:
Implementation cost + monthly license cost
The client will be able to monitor the quality of the fruit throughout the entire packing process, generating efficiencies and making timely decisions that result in greater income thanks to the digitalization of the process.
Future plans
In addition to the digitalization of quality evaluations with the user, reports are being implemented in Power BI that will allow greater data analysis in the packing plant to be able to make better decisions.
Among other cases that the company is evaluating implementing, "Packing efficiency control" is one that stands out.
By controlling plant efficiencies, the client will be able to determine which processes can be more efficient and identify bottlenecks per operation or operator. Also, they will be capable to analyze which are the critical points that generate economic losses due to low productivity and make decisions that allow generating efficiencies in the process.
Conclusions
- The client replaced traditional data capture methods using pencil and paper with SpaceAG's mobile application, managing to digitize the quality evaluations carried out in packing operations.
- Agroindustrial Beta obtained access to digital formats and reports to be able to monitor the quality of the fruit in real time. In this way, it could be more agile when sharing information with other areas or stakeholders.
- The client can now access traceability information more quickly, reducing the time for collecting and presenting information for internal and external audits by 30%.
Collect geo-located field data without internet connection.
Integrate and digitize all the data from your field and other systems.